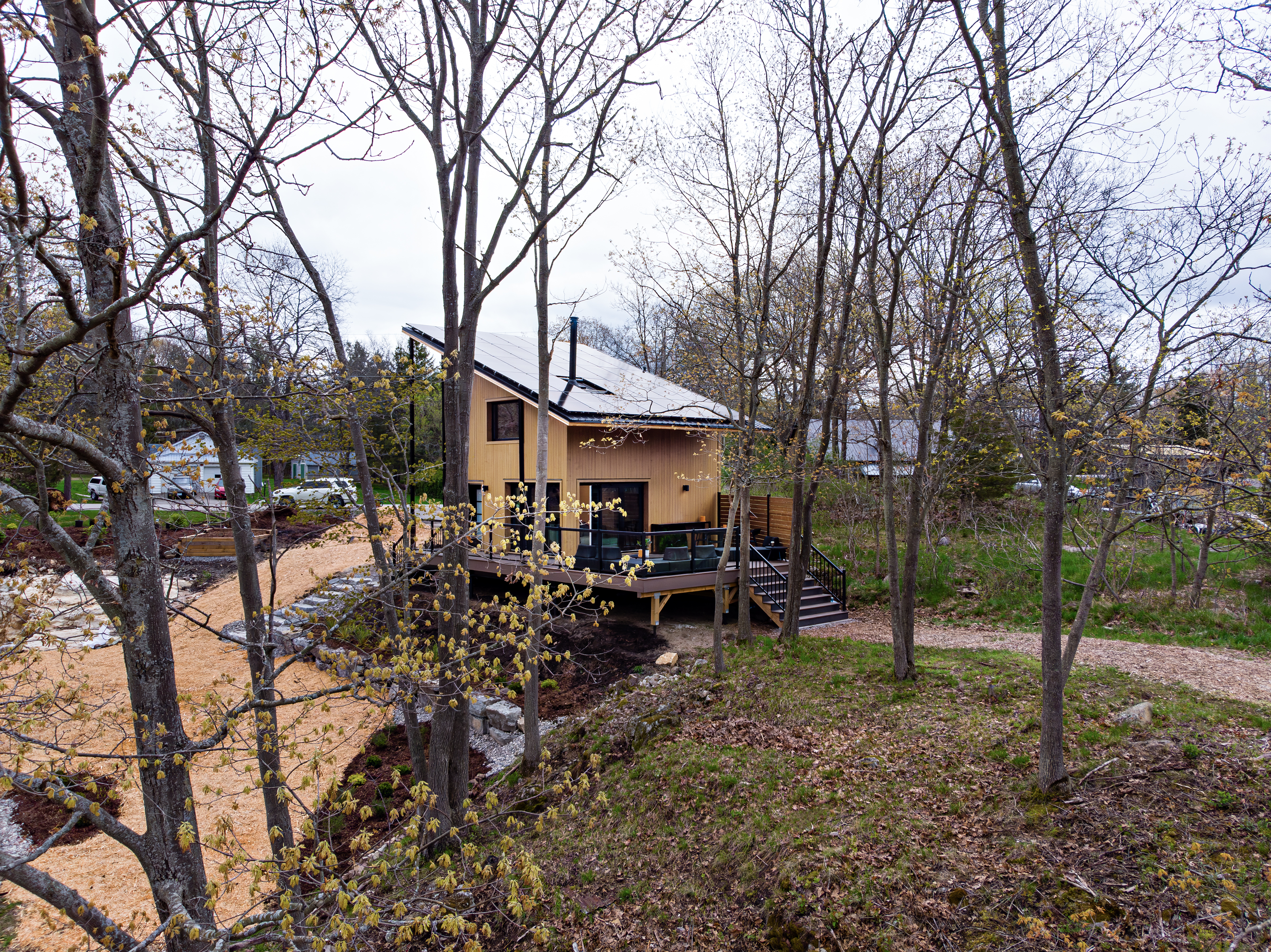
This article is part of a series called Transforming communities with Sustainable Affordable Housing. The series demonstrates how energy-efficient, community-centered housing can foster resilience and well-being. Discover practical solutions for affordable, climate-friendly homes that improve lives and build a sustainable future.
In Eastern Ontario, CABN has brought an ambitious vision to life with the completion of its first net-zero affordable home pilot, featuring a patent-pending energy-informed design mechanism. Supported by the Green Municipal Fund’s (GMF) Sustainable Affordable Housing (SAH) initiative, this project reimagines sustainable construction, paving the way for affordable housing solutions that are energy-efficient, low-maintenance, and replicable across Canada and beyond.
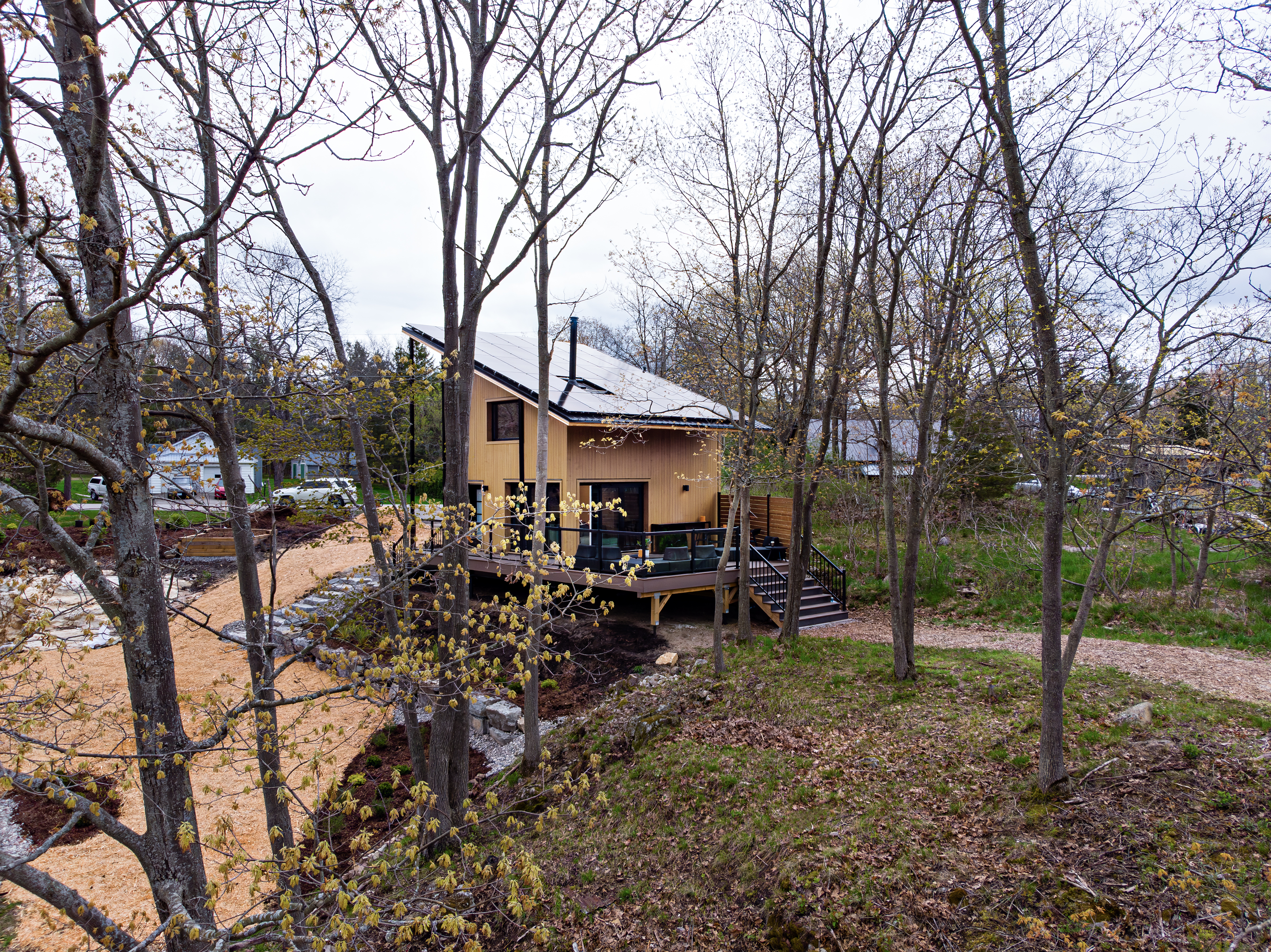
A fast and sustainable build
Despite beginning construction in the heart of winter, CABN completed the building’s core structure in just 48 hours, with final touches finished in a matter of weeks. This rapid construction proved the viability of building in extreme conditions, demonstrating that sustainable prefabricated housing is achievable even in remote or underserved areas.
Powered entirely by solar energy, the home operates with zero utility costs and consumes only 6,485 kWh annually—63 percent less energy than a typical passive house, a building standard focused on ultra-low energy use and high insulation.
“Our home uses 20 percent of the energy of a conventional build,” shared Alex Kelly, CABN’s Chief Operating Officer. “This creates new opportunities for communities to unlock land previously considered unfit for development.”
A community hub for innovation and learning
The pilot home serves as a community hub, engaging local leaders, housing providers, and builders to explore sustainable housing options. CABN hosted an open house for municipal officials and affordable housing providers to showcase the innovative design and encourage adoption in their own communities. Augusta Township’s leaders have expressed interest in expanding the project, potentially using municipal land for future developments.
Additionally, CABN established CABN Foundation, its non-profit arm, that partners with municipalities and developers to bring affordable, sustainable housing to remote, low-income, and Indigenous communities. For example, they are exploring partnerships with First Nations in Northern Ontario to build live-work housing for healthcare professionals.
“These homes come in prefabricated pieces—like a kit—allowing us to build quickly, even in areas with narrow construction windows,” Kelly explained.
This makes the model especially appealing to communities that face challenges like shorter building seasons or limited access due to ice road closures.
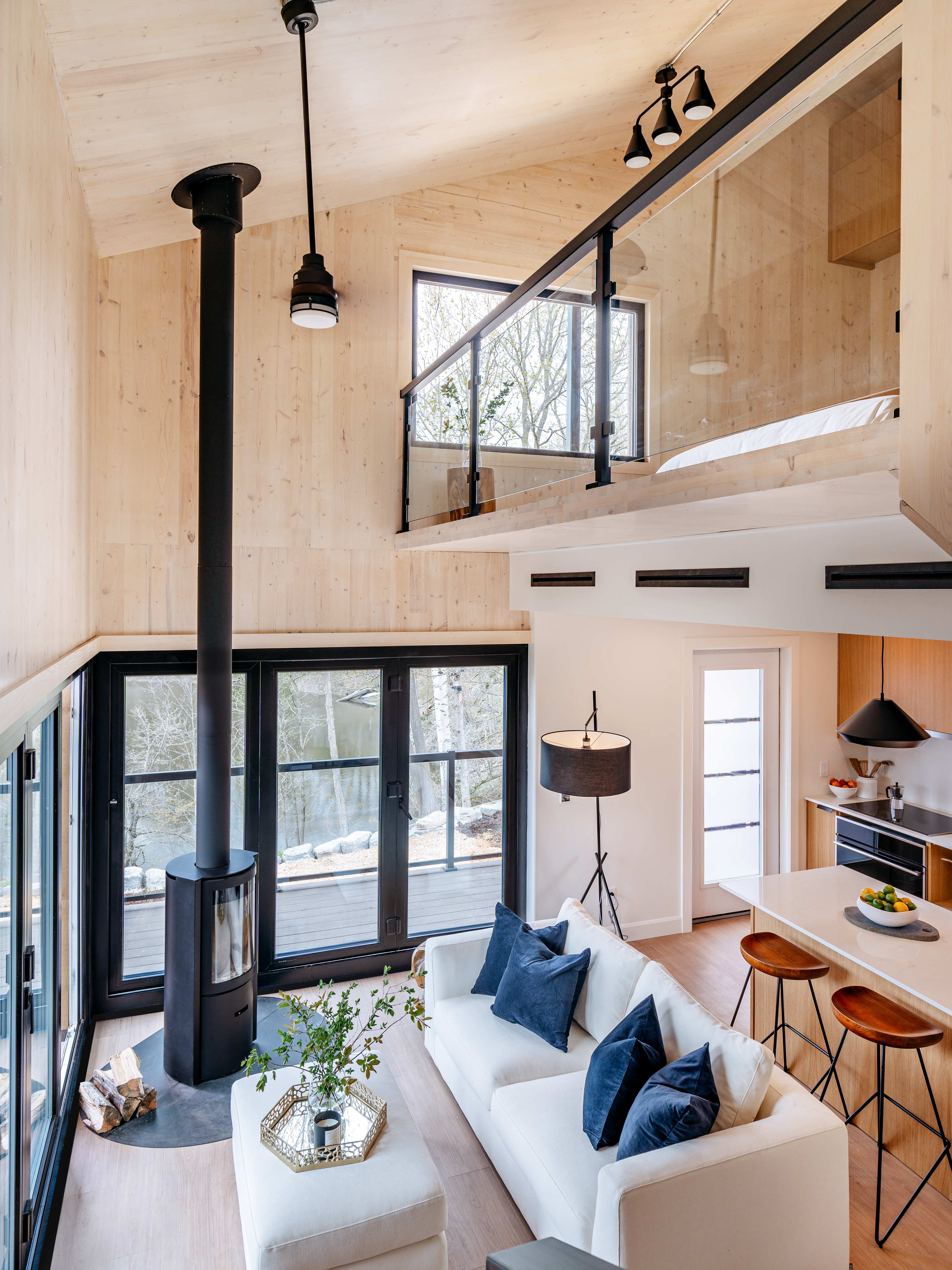
Environmental and financial impact
The environmental benefits of CABN’s design are significant. Compared to traditional builds, CABN produces 60 percent fewer greenhouse gas (GHG) emissions, thanks to the use of Forest Stewardship Council (FSC)-certified cross-laminated timber (CLT) for its walls, ceilings, and floors. For the pilot home alone, this resulted in a reduction of 3,393 kg of CO₂ emissions. Additionally, the home’s off-grid operation, powered by solar panels, avoids another 3,542 kg of CO₂ annually. These environmental savings scale dramatically in larger developments: a five-year production of 500 homes could prevent 47,000 tonnes of CO₂ emissions.
The financial impact is equally compelling. CABN's manufacturing processes—optimized through component-based design—promise a savings of up to $85 per square foot. Beyond construction, low maintenance requirements and zero energy costs offer significant savings to homeowners and housing providers.
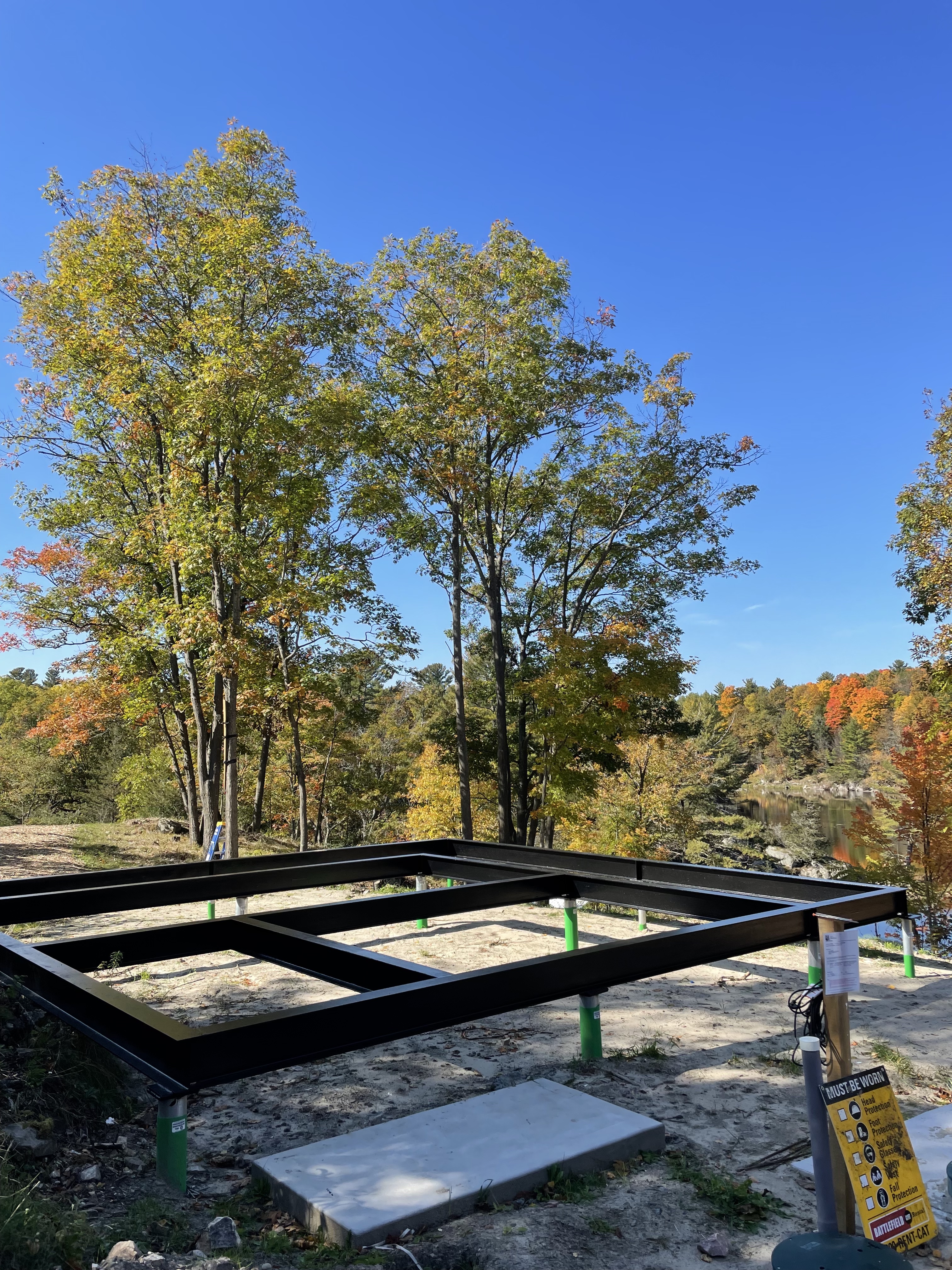
A model for replication and growth
The pilot project has proven that CABN’s approach is scalable and adaptable. The team is currently developing a multi-residential model to meet the needs of urban environments. This new design will allow for stacked townhouses or single-level apartments, accommodating diverse needs, including seniors and families with accessibility requirements.
Meanwhile, in Toronto, CABN is working with non-profit partners, such as Two Steps Home, to introduce transitional housing for individuals experiencing homelessness. This model features individual units surrounding shared amenities like kitchens and laundry facilities.
“Our goal with partners like Two Steps Home is to provide people with a secure place to live while they transition to more permanent housing solutions,” said Kelly.
CABN has also worked with the Community Housing Transformation Centre to develop a guidebook on creating sustainable, equitable housing communities. This resource will provide municipalities with a blueprint for integrating CABN’s model into their housing strategies, further driving innovation across the sector.
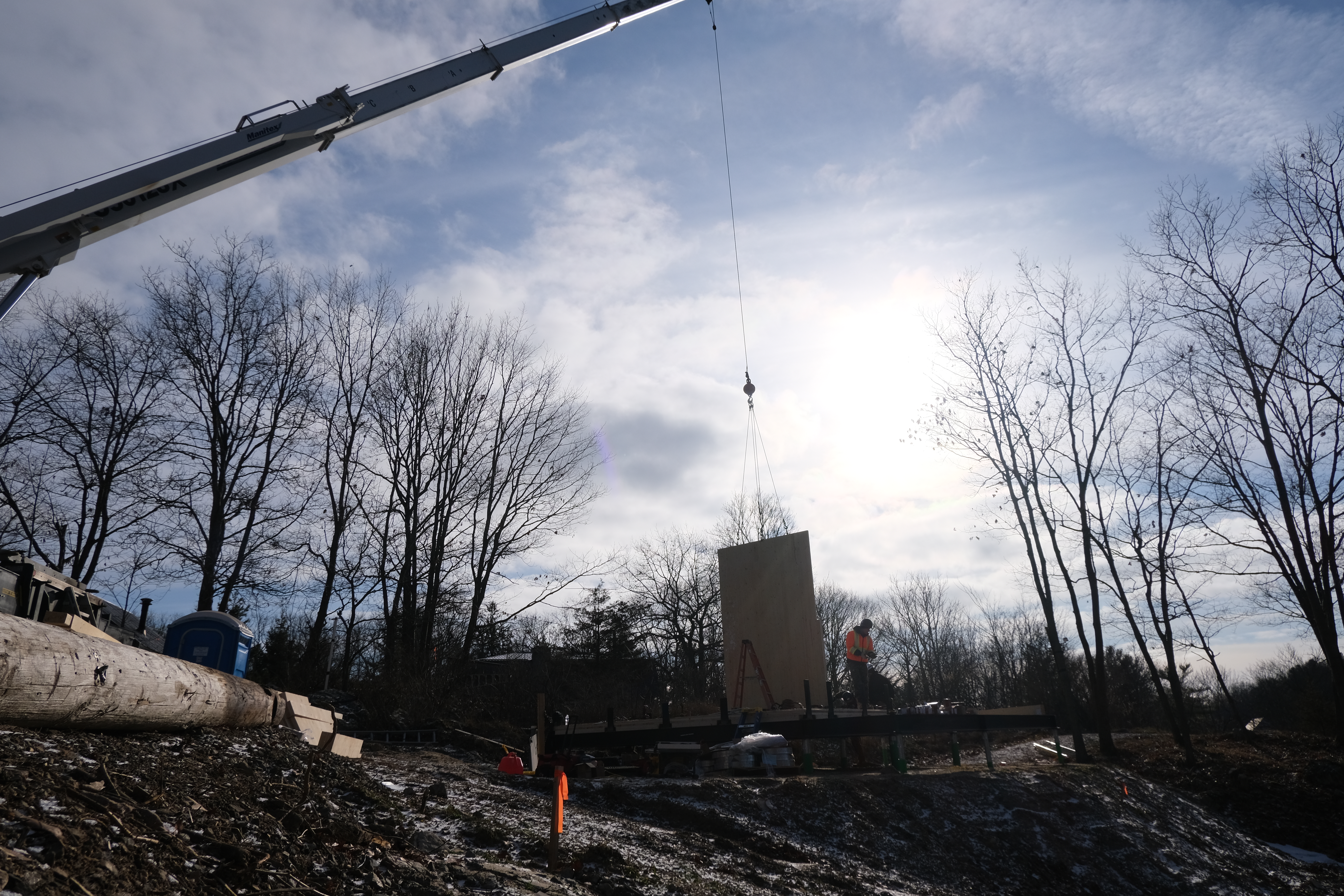
A future-focused approach
Looking ahead, CABN is expanding its partnerships to explore innovative materials and construction methods, such as alternative CLT materials—a sustainable, engineered wood product used for walls, ceilings and floors—including red pine and bamboo, as well as geothermal energy solutions. Collaborations with institutions like Carleton University further position CABN at the forefront of sustainable housing innovation.
As Augusta Township prepares for rapid population growth—fueled by new industry bringing considerable growth to the region—housing has become an urgent priority. CABN’s collaboration with the township to build a community of 67 units in a unique biomimicry-informed design, offers a sustainable and scalable solution to meet this rising demand. “The municipality has been actively seeking solutions—we’re excited to work with them on this,” Kelly noted.
From pilot to movement
What began as a single pilot home has become a catalyst for conversations about sustainable, affordable housing across Canada. The CABN project offers more than just shelter—it presents a blueprint for future communities, balancing environmental responsibility with economic and social impact.
“This project has been a springboard for incredible conversations and opportunities,” Kelly reflected. “It’s proof that sustainable, affordable housing isn’t just a dream—it’s a reality we can build today.”